Marc Leclair
Work Portfolio
Phase-Gate
New Product Development Process
I developed this NPDP for an organization that had, up to this point, performed their product release in a very informal manner. Formalizing the process helped departments define their roles & responsibilities. Problems would have quicker solutions, and quality products would release months earlier. Immature organizations revert to the idea that “we are all responsible to develop a good product”, but in reality, this simple idea makes the organization underperform during stressful times as no one individual has clear authority or accountability.
You see below that the colored boxes show the role of each department. The boxes themselves represent a document or record required during the design cycle. The triangles represent the gate reviews required during the design cycle. I’ve found consensus-based gate reviews to be the most practical.
I’ve used this model several times over. A formal NPDP speeed up time to market, gives executive management a clear view of an often messy design process, and makes the design team more efficient.
Visual Controls in the Workplace
The plain old picture of fans sitting on boxes (below) is evidence of a very powerful visual control in production.
The fan final assembly process is a “simple” manual light assembly process. To make a final assembly part, we choose: the base fan, the power cord, the fan ring and the fan blade. In pursuit of operational excellence, we made many improvements to this line which improved efficiency and decreased our rate of out-of-box failure.
However, one out of box defect remained. Orders would ship where several fans would not have fan blades. After much investigation, we treated fan blades as a visual control point. We would kit out the exact quantity of fan blades with each order - as always. BUT, if assemblers got to the end of the job with extra fan blades, our process now required the team to breakdown the shipping palate and inspect the fans to ensure that all fans had blades.
From this point on, our failure rate was near-flawless. We would run for months without a reported effect. So what was the problem? Assemblers would sometimes miss the fan blade assembly step on a few fans when they would come back from break or lunch. Formerly if there were fan blades left over, the assumption was miscount and the assembler would return extra blades to inventory.
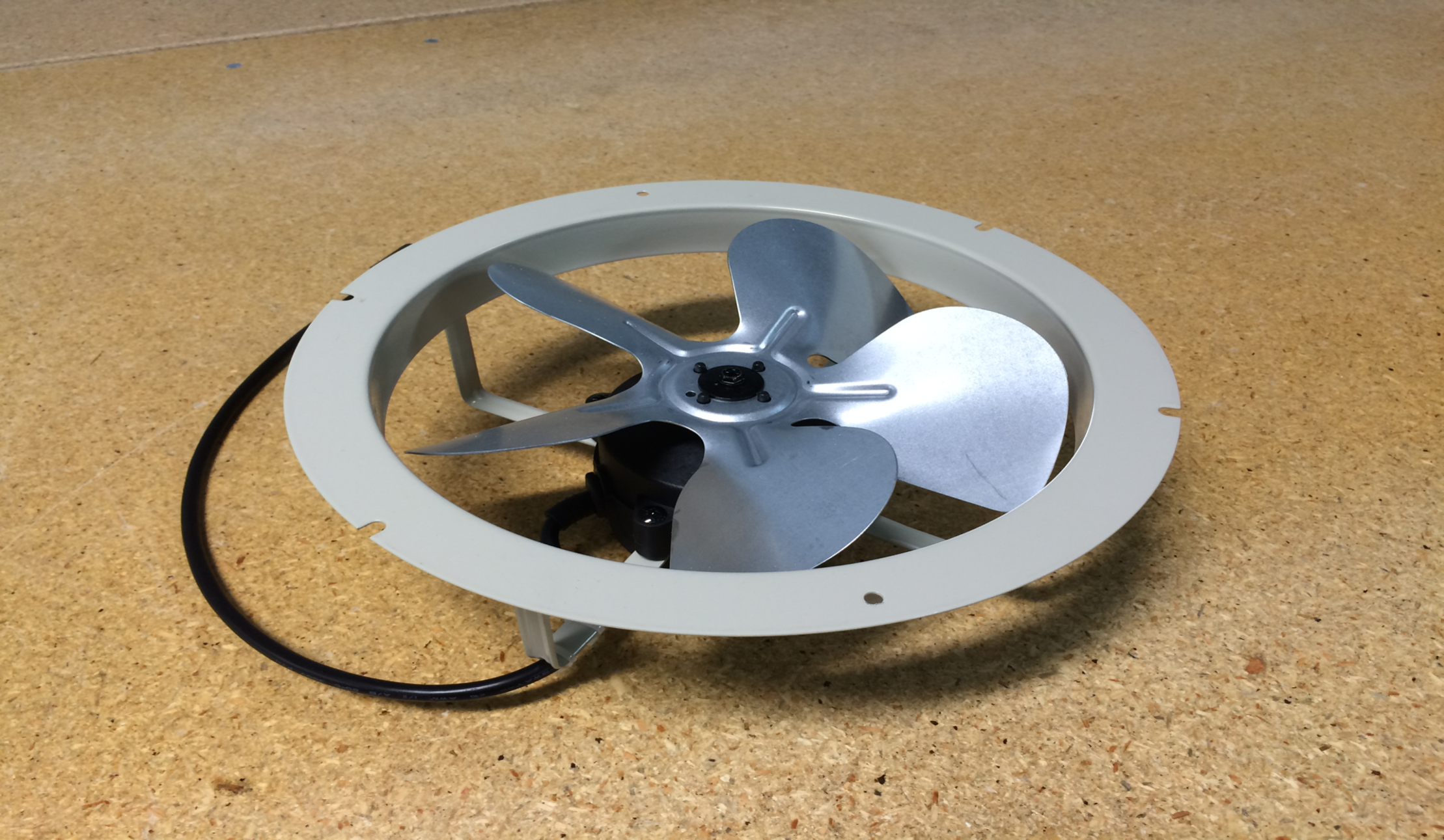
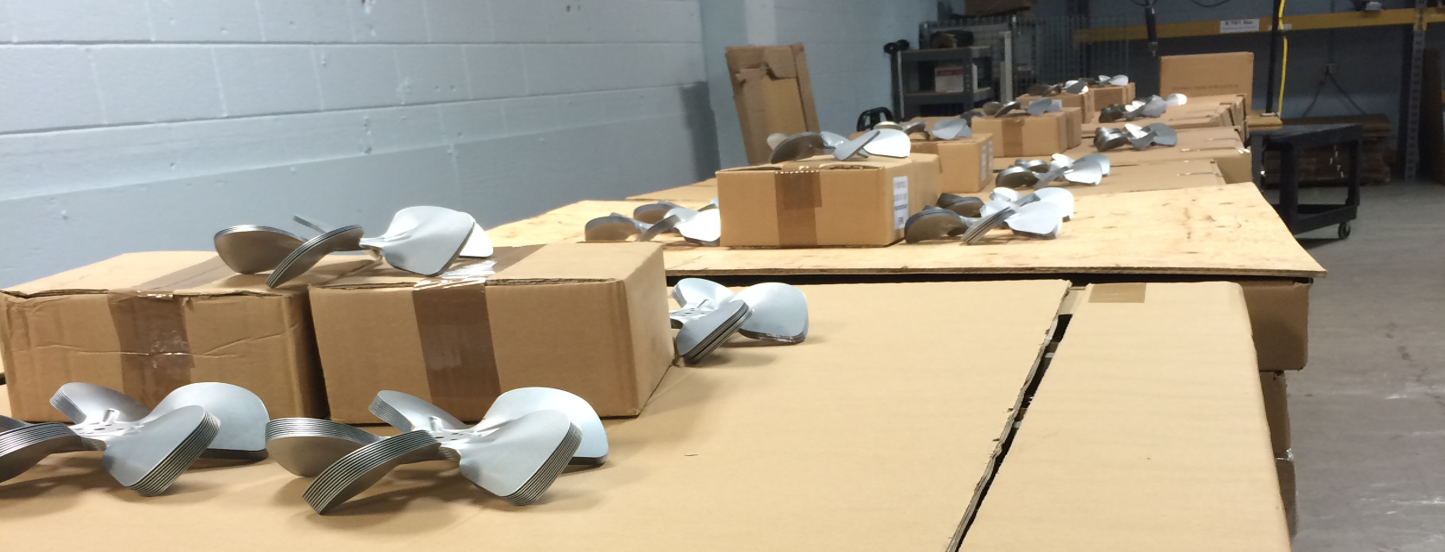
Lean Manufacturing Workstation
In the photo , you can see several elements of lean manufacturing which helped to improve product quality and efficiency.
Torque Driver
The torque driver with the articulating torque arms ensures that fasteners are tightened to exact requirements. The driver is places at a height which is convenient to the operator to limit stress and movement.Assembly fixture
The assembly fixture simplifies the assembly steps and employs Poka-yoke to prevent the fan mounting ring from mis-orientation.Worksurface
The worksurface is clear of all extraneous objects. The only objects allowed on the worksurface are the items actively in use: products and tools.Shadow board
The simple shadow board is a powerful tool. It provides storage and visual organization. It also offers easy traceability and accountability when items go missing.Wheels
Both the shadow board and the workbench are provisioned with lockable wheels. This offers easy confgurability as production staffing and staging change.
Workforce Development
We’ve all heard the platitude “People are our most important asset”. This is so easy to say, but difficult to live by. If we can harness the skills and experience of the workforce in a mutually beneficial way, we all win, right?
I’ve put together career development steps for my production workers. The steps take someone from new in their career all the way to being a production supervisor. As the individual develops skills, become a more valuable worker thus, they are eligible for raises or promotions. This system makes the reward system quite objective, so it is less often that employees feel ignored or treated unfairly, because everyone see what the employer values, and it takes for them to progress in their career.
Publications
Thesis: Quality Assurance for Competitiveness
I wrote my thesis as part of my Master’s Degree in Quality Assurance. The actual title is QUALITY ASSURANCE STRATEGIES FOR THE ORGANIZATION IN TRANSITION. I chose my subject matter so that I could prove to myself (and others) that QA created value for an organization and applied correctly, QA could be a competitive advantage.
The Seven Deadly Sins of Supplier Development
This is a discussion about things often done for expediency’s sake, but in the long term create underperformance and disfunction in the supplier-customer relationship.
Blog Post: Root-Cause Analysis Starts with a Good Problem Statement
A problem is merely the difference between the way things are and the way things need to be. The difficulty in writing a good problem statement often stems from knowing too much. With a good problem statement, we focus our team with on the issue that needs attention.
Blog Post: Determining Root-Cause through the Five Whys
Beginners often struggle with the five whys. They are easy to learn, but difficult to master. Let’s discuss the make-up of a good five why.
The 8D Problem Solving Approach
My presentation was a discussion on real-world practices using the 8D Process for Problem Solving. Presented to the Dallas-Ft Worth Biomedical Discussion Group, 21 Jan 2015.
Executive Quality Roundtable Summary
On Tuesday, October 9th 2012, ASQ Charlotte assembled twenty three executives for the inaugural Executive Quality Roundtable. These executives represented manufacturing, food and beverage, healthcare, banking, insurance, finance, retail, software, and educational organizations throughout the greater Charlotte-Mecklenburg area .Coca Cola Consolidated (EQR) hosted this invitation-only peer-to-peer learning event, where the common denominator across the executive participants was senior leaders who are passionate about driving sustained quality improvement in their organizations and our community.
Getting the Most from Supplier Audits
Many organizations recognize supplier audits as a valuable business tool. Supplier audits help us deliver quality products on time, under budget. A successful supplier audit often has many benefits.
Stop Sending Supplier Surveys
So other than fulfilling the ISO 9001 Quality requirement, how has this effort of collecting supplier surveys helped your company to be competitive or provide value to your customers?
Frequently Asked Questions
-
Yes:
Datamax
Removed entire backlog of discrepant parts by creating a repair rubric & incentive system for repair technicians. Eliminated $1M from field service inventory and reduced repair turn time from weeks to days.
Zebra
Performed analysis of RMA & Warranty repair causes. Worked with Manufacturing and Design Engineering to eliminate causes of warranty failures. Repair depot reduced from 10 technicians to three.SourceTech
As lead technical liaison, I preserved a $6M high margin service contract by providing superior analysis of field failures and training Version techs on simple repair method that they could perform on site.Epec
Instituted rigorous test and inspection steps that eliminated out of box failures and warranty returns. While company doubled in revenue, repair labor stayed neutral.Patrol PC
Responsible for installation & service calls on computers & communication systems for 1st Responder Vehicles. -
Early career Test Engineer at Mars Electronics where we ran both a SMD & Through Hole lines. Influenced product testability, designed test fixtures, and diagnosed production PCBA failures.
Evaluated PCBA suppliers locally, and globally for capability of equipment & processes. Worked to develop supplier capability to reduce manufacturing fallout.
Initiated & followed up on PCBA supplier corrective actions to increase incoming product yield.
Evaluate supplier PCBA fallout to initiate design, process or specification changes.
I am versed in IPC specs 600, 610, 620 and J STD 100, among others.
At Epec worked with customers to evaluate and resolve PCB discrepancies.
My most stringent production was passive microwave devices we manufactured for the US Navy. I called our spec Class III plus because it was so exacting - beyond IPC 610 class III.
-Example of SMT expertise:
Videology had a long-standing issue with BGA solderability on one particular product. The entire crew at Videology kept blaming the assembly house. Shortly after I started. I dug in to the problem. The assembly house was unhelpful and adversarial because Videology sources their own PCBs for production and the assembly house suspected PCB quality. I sent a PCB out for analysis. I found that the gold was ½ of the IPC spec and Videology did not the spec gold thickness. I changed the spec to two microinches. Problem solved production yield was at 1000/1000. -
Yes
As VP of Operations, I have run three US manufacturing sites concurrently. In one instance I also ran a manufacturing plant in The Netherlands.
